3D-printing objects containing multiple metals and alloys
July 29, 2014
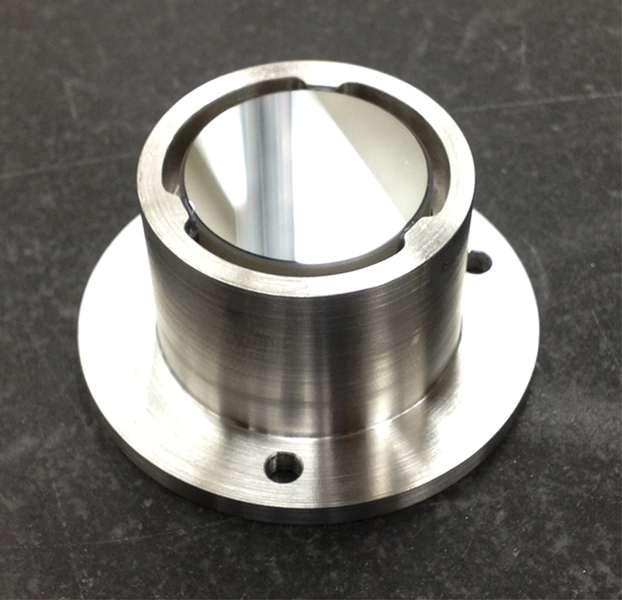
A prototype of a mirror mount made using a new multi-material 3D printing technique (credit: NASA-JPL/Caltech)
Researchers at NASA‘s Jet Propulsion Laboratory (JPL), California Institute of Technology, and Pennsylvania State University have developed a 3D printing process that transitions from one metal or alloy to another in a single object.
For example, they created a prototype of an improved telescope mirror mount. The part at the top near the glass mirror is made of a metal with low thermal expansion, so that it won’t shrink in space as much as most metals do. That prevents stress in the epoxy adhesive between the mirror and the metal. The bottom part of this mount is stronger stainless steel and could be connected to a stainless steel component of a spacecraft.
The new multi-material additive manufacturing process
Using a laser to melt metal powder, the researchers deposit layers of metal on a rotating rod, thus transitioning metals radially (from the inside out, rather than adding layers from bottom to top, as in the traditional 3D printing technique.
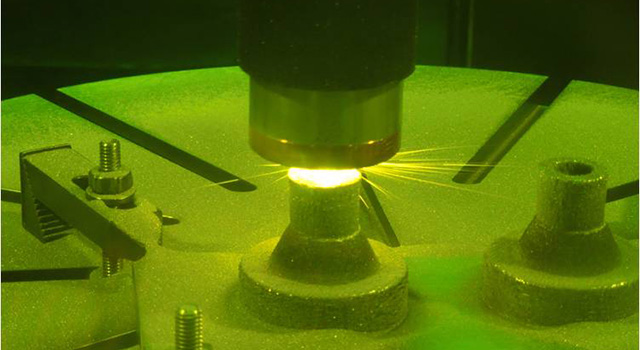
A rocket nozzle made using a new 3D printing technique that allows for multiple metallic properties in the same object (credit: NASA-JPL/Caltech)
Of course, you could separately make both halves of the object from their respective metals and then weld them together. But the weld itself may be brittle, so that your new object might fall apart under stress. That’s not a good idea if you are constructing an interplanetary spacecraft, for example, which cannot be fixed once it is deployed.
Future space missions may incorporate parts made with this technique. One key use that NASA has identified is for making metal inserts with a low coefficient of thermal expansion for carbon-fiber spacecraft panels, as shown in the two illustrations below.
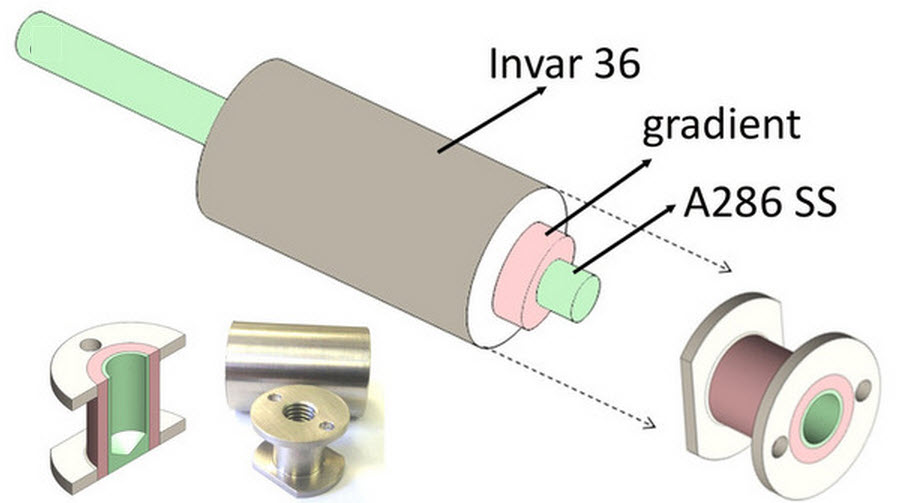
Schematic of how gradient alloys were machined from a radially graded rod. The core of the alloy was constructed of A286 stainless steel, used in bolts on some spacecraft. The exterior of the rod, Invar 36, was selected because it exhibits a low coefficient of expansion, matching that of a carbon-fiber panel (into which the part was to be inserted). To transition the stainless steel to the Invar coating, a gradient 304 L stainless steel was deposited directly onto the A286 bolt in a step-function gradient. (Credit: Douglas C. Hofmann et al./Scientific Reports)
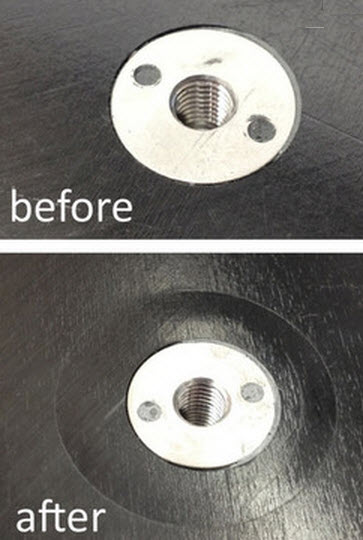
Addition of Invar 36 material and gradient material around the rod to transition the stainless steel material to the carbon-fiber-panel coefficient of expansion (credit: Douglas C. Hofmann et al./Scientific Reports)
The auto industry and the commercial aerospace industry may also find it useful, according to the researchers.
A report on this work was published in Scientific Reports (open access). The work was funded by NASA. Caltech manages JPL for NASA.
Abstract of Scientific Reports paper
Interest in additive manufacturing (AM) has dramatically expanded in the last several years, owing to the paradigm shift that the process provides over conventional manufacturing. Although the vast majority of recent work in AM has focused on three-dimensional printing in polymers, AM techniques for fabricating metal alloys have been available for more than a decade. Here, laser deposition (LD) is used to fabricate multifunctional metal alloys that have a strategically graded composition to alter their mechanical and physical properties. Using the technique in combination with rotational deposition enables fabrication of compositional gradients radially from the center of a sample. A roadmap for developing gradient alloys is presented that uses multi-component phase diagrams as maps for composition selection so as to avoid unwanted phases. Practical applications for the new technology are demonstrated in low-coefficient of thermal expansion radially graded metal inserts for carbon-fiber spacecraft panels.