A practical solution to mass-producing low-cost nanoparticles
February 26, 2016
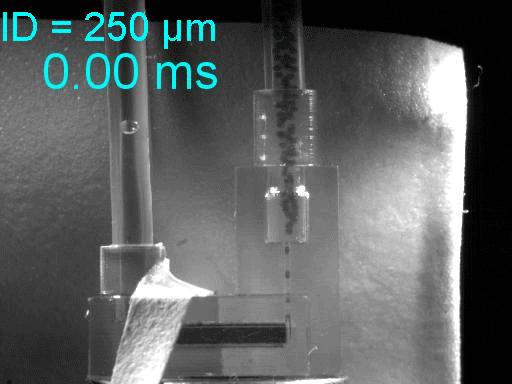
Nanoparticles form in a 3-D-printed microfluidic channel. Each droplet shown here is about 250 micrometers in diameter, and contains billions of platinum nanoparticles. (credit: Richard Brutchey and Noah Malmstadt/USC)
USC researchers have created an automated method of manufacturing nanoparticles that may transform the process from an expensive, painstaking, batch-by-batch process by a technician in a chemistry lab, mixing up a batch of chemicals by hand in traditional lab flasks and beakers.
Consider, for example, gold nanoparticles. Their ability to slip through the cell’s membrane makes them ideal delivery devices for medications to healthy cells, or fatal doses of radiation to cancer cells. But the price of gold nanoparticles at $80,000 per gram, compared to about $50 for pure raw gold goes.
The solution, published in an open access paper in Nature Communications on Feb. 23, is microfluidics — manipulating tiny droplets of fluid in narrow channels. The team 3D-printed tubes about 250 micrometers in diameter, possibly the smallest, fully enclosed 3D printed tubes anywhere.
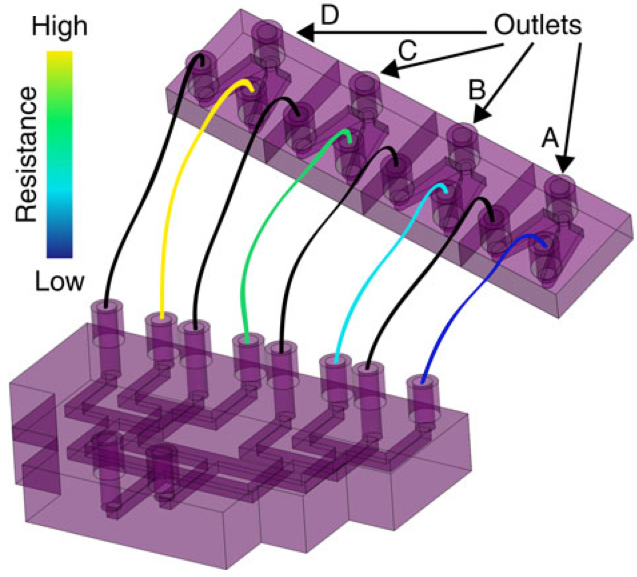
Droplet formation for stable parallel microreactors (credit: Carson T. Riche et al./Nature Communications)
Then they built a parallel network of four of these tubes, side-by-side, and ran a combination of two non-mixing fluids (like oil and water) through them. As the two fluids fought to get out through the openings, they squeezed off tiny droplets. Each of these droplets acted as a microscale chemical reactor in which materials were mixed and nanoparticles were generated. Each microfluidic tube can create millions of identical droplets that perform the same reaction.
This sort of exotic process has been envisioned in the past, but its hasn’t been able to be scaled up because the parallel structure meant that if one tube got jammed, it would cause a ripple effect of changing pressures along its neighbors, knocking out the entire system.
The researchers bypassed this problem by altering the geometry of the tubes themselves, shaping the junction between the tubes such that the particles come out a uniform size and the system is immune to pressure changes.
The work was supported by the National Science Foundation.
USC | Nanoparticle Production
Abstract of Flow invariant droplet formation for stable parallel microreactors
The translation of batch chemistries onto continuous flow platforms requires addressing the issues of consistent fluidic behaviour, channel fouling and high-throughput processing. Droplet microfluidic technologies reduce channel fouling and provide an improved level of control over heat and mass transfer to control reaction kinetics. However, in conventional geometries, the droplet size is sensitive to changes in flow rates. Here we report a three-dimensional droplet generating device that exhibits flow invariant behaviour and is robust to fluctuations in flow rate. In addition, the droplet generator is capable of producing droplet volumes spanning four orders of magnitude. We apply this device in a parallel network to synthesize platinum nanoparticles using an ionic liquid solvent, demonstrate reproducible synthesis after recycling the ionic liquid, and double the reaction yield compared with an analogous batch synthesis.