A robotic insect makes first controlled test flight
May 9, 2013
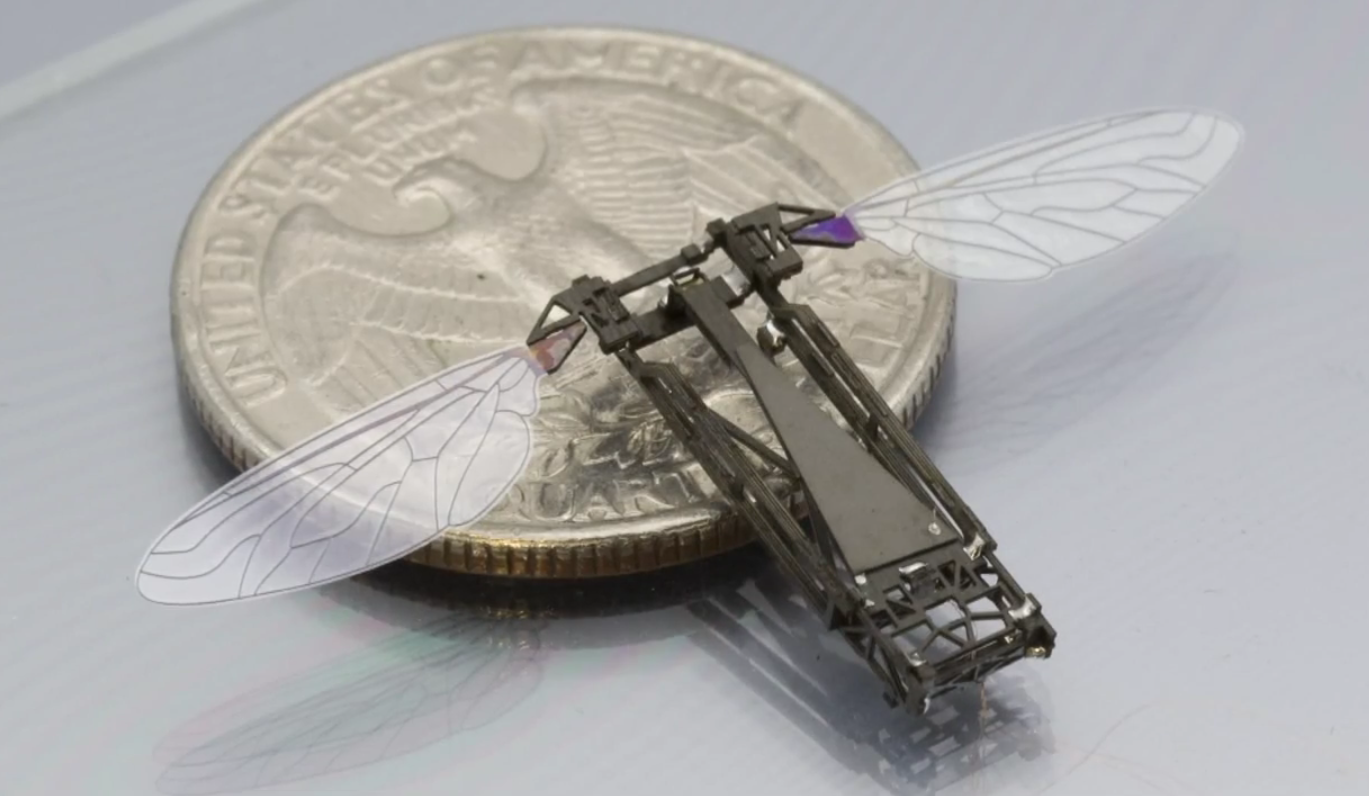
Robotic insect (credit: Harvard University)
Harvard roboticists have created a robotic insect the size of a paper clip and successfully test-flown it.
Inspired by the biology of a fly, the intricate design is the culmination of 12 years of painstaking work by researchers at the Harvard School of Engineering and Applied Sciences (SEAS) and the Wyss Institute for Biologically Inspired Engineering at Harvard.
The device represents the cutting edge of micromanufacturing and control systems, says Robert J. Wood, Charles River Professor of Engineering and Applied Sciences at SEAS, Wyss core faculty member, and principal investigator of the National Science Foundation-supported RoboBee project.
Inventing microscale aeronautics
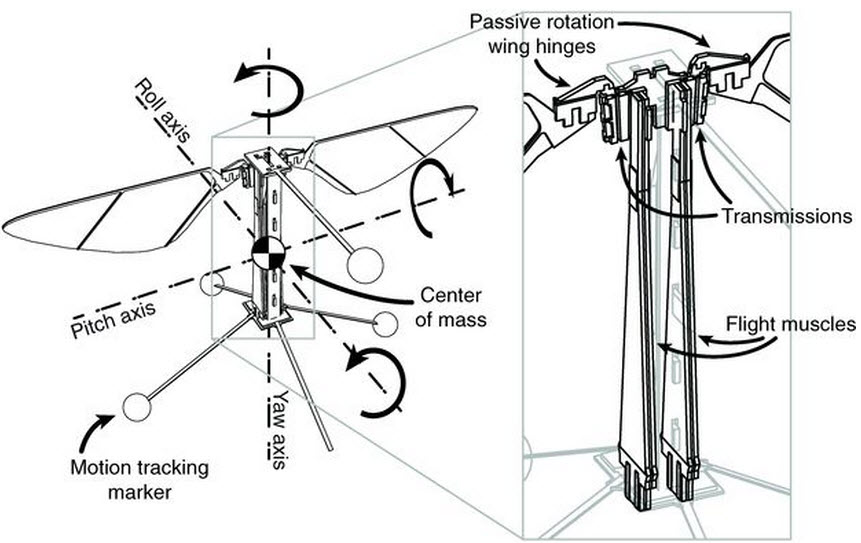
An ingenious design. Eight infrared, motion tracking cameras observe the positions of retroreflective markers attached to the robot to estimate its position and orientation in space with low latency. Position estimates are transmitted to the controller computer, which computes the control signals and sends them to the robot via a wire tether. Each wing can be controlled independently. The 3 rotational degrees of freedom of the fly are simplified in the robotic fly to a reciprocating flapping motion. (Credit: Kevin Y. Ma et al./Science)
At those insect-size dimensions and weight, the researchers had to thrown out the book and reinvent the science of flight at the microscale.
The microrobot has submillimeter-scale anatomy and two wafer-thin wings that flap almost invisibly at 120 Hz (times per second) — close to the fly’s 130 Hz. It weighs just 80 milligrams. The tiny robot flaps its wings with piezoelectric actuators — strips of ceramic that expand and contract when an electric field is applied.
At these tiny scales, small changes in airflow can have an outsized effect on flight dynamics, and the control system has to react that much faster to remain stable. Thin hinges of plastic embedded within the carbon fiber body frame serve as joints, and a delicately balanced control system commands the rotational motions in the flapping-wing robot, with each wing controlled independently in real time.
The robotic insects also take advantage of an ingenious pop-up manufacturing technique that was developed by Wood’s team in 2011. Sheets of various laser-cut materials are layered and sandwiched together into a thin, flat plate that folds up like a child’s pop-up book into the complete electromechanical structure.
Applications
The robotic insect could be useful in distributed environmental monitoring, search-and-rescue operations, and assistance with crop pollination, for example, but the materials, fabrication techniques, and components that emerge along the way might prove to be even more significant.
For example, the pop-up manufacturing process could enable a new class of complex medical devices. Harvard’s Office of Technology Development, in collaboration with Harvard SEAS and the Wyss Institute, is already in the process of commercializing some of the underlying technologies.
Next steps will include developing the brain, the colony coordination behavior, the power source, and other subsystems required to make the robotic insects fully autonomous and wireless.
The prototypes are still tethered by a very thin power cable because there are no off-the-shelf solutions for energy storage that are small enough to be mounted on the robot’s body. High-energy-density fuel cells must be developed before the RoboBees will be able to fly with much independence.
“This project provides a common motivation for scientists and engineers across the University to build smaller batteries, to design more efficient control systems, and to create stronger, more lightweight materials,” says Wood.