Regenerating plastic material grows back after damage
May 12, 2014
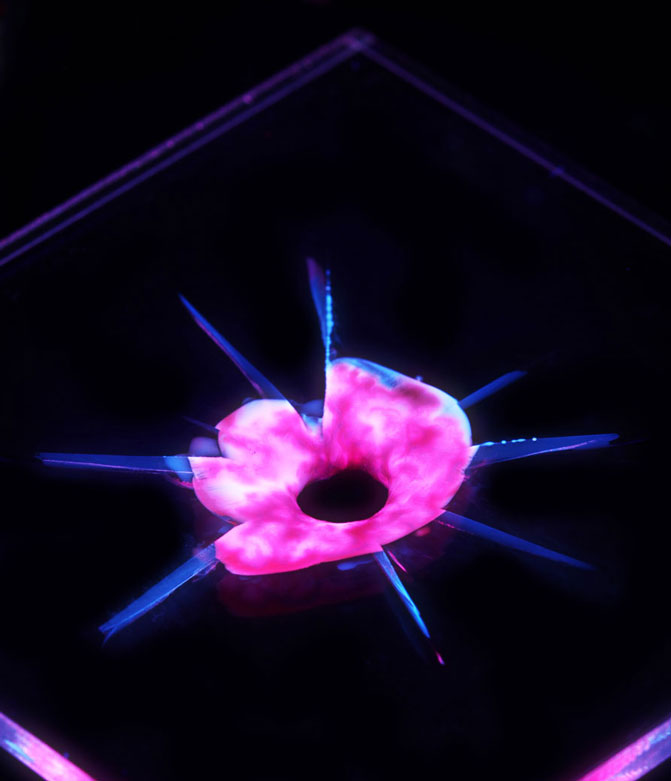
Illinois researchers have developed materials that not only heal, but regenerate. The restorative material is delivered through two isolated fluid streams (dyed red and blue). The combined liquid immediately gels and later hardens, resulting in recovery of the entire damaged region. This image is halfway through the restoration process. (Credit: University of Illinois)
University of Illinois researchers have developed self-repairing materials that not only heal, but also regenerate.
Until now, self-repairing materials (such as the “terminator” polymer) could only bond tiny microscopic cracks. The new materials fill in large cracks and holes by regrowing material.
“We have demonstrated repair of a nonliving, synthetic materials system in a way that is reminiscent of repair-by-regrowth as seen in some living systems,” said Jeffry S. Moore, a professor of chemistry.
Such self-repair capabilities would be a boon for commercial goods — imagine a mangled car bumper that repairs itself within minutes of an accident — and especially for parts and products that are difficult to replace or repair, such as those used in aerospace applications.
Vascular delivery
The regenerating capabilities build on the team’s previous work in developing vascular (blood-vessel-like) materials. Using specially formulated fibers that disintegrate, the researchers can create materials with networks of capillaries inspired by biological circulatory systems.
The vascular delivery allows for delivering a large volume of healing agents — which, in turn, enables restoration of large damage zones, which also enables multiple restorations if the material is damaged more than once.
Two adjoining, parallel capillaries are filled with regenerative chemicals that flow out when damage occurs. The two liquids mix to form a gel, which spans the gap caused by damage, filling in cracks and holes. Then the gel hardens into a strong polymer, restoring the plastic’s mechanical strength.
“We have to battle a lot of extrinsic factors for regeneration, including gravity,” said study leader Scott White, a professor of aerospace engineering. “The reactive liquids we use form a gel fairly quickly, so that as it’s released it starts to harden immediately. If it didn’t, the liquids would just pour out of the damaged area and you’d essentially bleed out. Because it forms a gel, it supports and retains the fluids. Since it’s not a structural material at that point yet, we can continue the regrowth process by pumping more fluid into the hole.”
Tuning the healing time
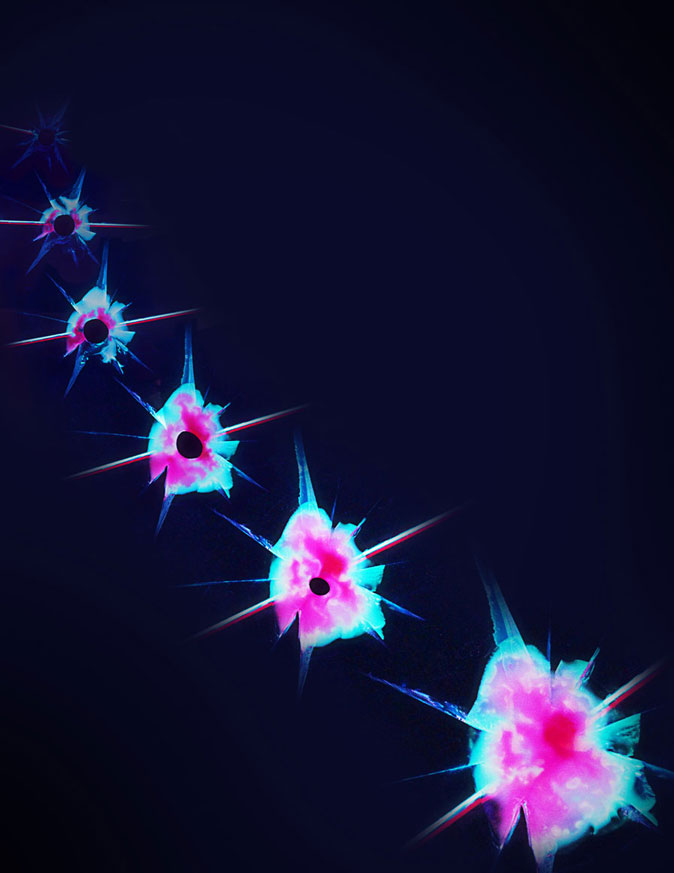
Time sequence of overhead images of an impact-damaged specimen undergoing the restoration process. The restorative process begins (top left) with the delivery of material through two, isolated fluid streams (dyed red and blue) that infiltrates the cracks and wets the inner surface of the damage. The fluid quickly transitions to a gel, which acts as a scaffold for the continuing delivery of restorative materials. After the damaged specimen has completely recovered (bottom right), the gel undergoes another transition to a rigid, structural solid, completing the restoration process and returning the damaged material to its original function. (Credit: Nathan Bajandas)
The team demonstrated their regenerating system on the two biggest classes of commercial plastics: thermoplastics and thermosets. The researchers can tune the chemical reactions to control the speed of the gel formation or the speed of the hardening, depending on the kind of damage.
For example, a bullet impact might cause a radiating series of cracks as well as a central hole, so the gel reaction could be slowed to allow the chemicals to seep into the cracks before hardening.
The researchers envision commercial plastics and polymers with vascular networks filled with regenerative agents ready to be deployed whenever damage occurs, much like biological healing. T
heir previous work established ease of manufacturing, so now they are working to optimize the regenerative chemical systems for different types of materials.
“For the first time, we’ve shown that you can regenerate lost material in a structural polymer. That’s the kicker here,” White said, “Prior to this work, if you cut off a piece of material, it’s gone. Now we’ve shown that the material can actually regrow.”
It might be interesting to combine this regenerative process with MIT’s “twinning” process, also bio-inspired, which keeps the damage from spreading outward. So a bullet hole in a windshield might disappear — actual “terminator”-style.
“Previous self-healing approaches were limited to addressing damage with approximately 100 micron crack separations, co-author Brett Krull, graduate student in materials science and engineering, told KurzweilAI in an email interview. “In this work, we’re increasing that repair ability by a factor of 100. We’ve been able to repair holes up to 9 mm and impact damage up to 35 mm diameter in a process reminiscent of regrowth in biological regeneration.
“We hope this research will be a starting point for the development of materials that continuously regenerate and remodel. We are just at the beginning of the development process, but the long-term, far reaching goal is to develop materials with vastly extended life cycles.”
The Air Force Office of Scientific Research supported this work.
Professor Scott White discusses the research breakthrough that allows plastic to not only heal, but truly regenerate.
Self-healing materials have been around for about a decade. But they have never been able to heal damage much larger than the width of a human hair. But now, White and his colleagues Jeff Moore and Nancy Sottos have developed plastic that can regenerate damage as large as a bullet hole.
The plastic regenerates when two chemical channels in the material mix at a damaged area. This reaction forms a gel which fills in the hole and eventually hardens, similar to blood clotting in a wound.
White is a professor of aerospace engineering at the University of Illinois at Urbana-Champaign and a member of the Autonomous Materials Systems group at the Beckman Institute for Advanced Science and Technology.
Abstract of Science paper
The regenerative power of tissues and organs in biology has no analog in synthetic materials. Although self-healing of microscopic defects has been demonstrated, the regrowth of material lost through catastrophic damage requires a regenerative-like approach. We demonstrate a vascular synthetic system that restores mechanical performance in response to large-scale damage. Gap-filling scaffolds are created through a two-stage polymer chemistry that initially forms a shape-conforming dynamic gel but later polymerizes to a solid structural polymer with robust mechanical properties. Through the control of reaction kinetics and vascular delivery rate, we filled impacted regions that exceed 35 mm in diameter within 20 min and restored mechanical function within 3 hours. After restoration of impact damage, 62% of the total absorbed energy was recovered in comparison with that in initial impact tests.